Great insight, as always. Thank you. That gave me the confidence to plug it into the Lisa 2/10 and sure enough, it works just fine under Lisa Office System. The tracking speed is incredibly slow, however, and it wouldn't be practical to use unless that tracking speed can be adjusted.
Here it is in use: https://www.youtube.com/watch?v=oGRYXVdL5j8
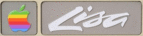
LisaList2
- May 01, 2024, 05:48:08 pm
- Welcome, Guest
News:
2022.06.03 added links to LisaList1 and LisaFAQ to the General Category
11
on: April 21, 2024, 04:18:21 pm
|
||
Started by ried - Last post by ried | ||
12
on: April 21, 2024, 03:08:15 pm
|
||
Started by ried - Last post by sigma7 | ||
first-generation Kensington Turbo Mouse 62350 trackball... features all 9 pins in its connector, unlike the Lisa's A9M0050 mouse and the M0100 mouse, where pin 6 is missing. Pin 6 is an input for a third mouse button (which is not supported by any software that I know of). Since the trackball is powered by 5V and the input is tolerant of voltages 0 to 5V, I can't imagine an electronic problem could arise. However, pin 6 of the mouse port is also connected to pin 25 of the back panel parallel port of the Lisa 1/2 (not connected to the parallel port in the 2/10), and designated "CHK" on the schematic. I believe this isn't used by the ProFile (perhaps it is for use by a parallel printer -- anyone know?), but it might be wise to check the voltage on pin 6 of the mouse port if you have something attached to the back panel parallel port. If you don't mind opening the trackball, I'd guess you'll find that there is nothing connected to that pin, so starting there may eliminate any worry. HTH |
13
on: April 21, 2024, 01:05:19 pm
|
||
Started by ried - Last post by ried | ||
I picked up a first-generation Kensington Turbo Mouse 62350 trackball recently, which was made for the Macintosh 128K. It has the same 9-pin D-SUB (DB9) connector as the Macintosh's original Apple M0100 mouse. However, the Kensington trackball features all 9 pins in its connector, unlike the Lisa's A9M0050 mouse and the M0100 mouse, where pin 6 is missing.
Is there any danger in plugging this Kensington's fully populated 9-pin connector into my Lisa 2/10? Will the Kensington's pin 6 cause any potential damage to the Lisa? I'm guessing no, but figured I would ask those more knowledgeable before curiosity gets the better of me. I would like to see this trackball working with Lisa Office System ![]() Pictures here: https://imgur.com/a/djxnspg |
14
on: April 20, 2024, 11:18:40 am
|
||
Started by ried - Last post by ried | ||
The guy helping to facilitate major discoveries?
![]() Maybe he learned some keyboard shortcuts, turned to the camera and thought to himself "Now I'm really going to get stuff done, guys." |
15
on: April 20, 2024, 02:14:10 am
|
||
Started by ried - Last post by stepleton | ||
Looking at the video, I could've been fooled if you'd told me it was a slide projector and an audio cassette. That part where the guy turns his head to face the camera is memorable...
|
16
on: April 19, 2024, 06:57:12 pm
|
||
Started by ried - Last post by ried | ||
This was on a plain ol' VHS tape.
|
17
on: April 19, 2024, 02:14:35 pm
|
||
Started by ried - Last post by blusnowkitty | ||
Where'd you find a U-matic deck to play it on?
Cool video though - pay close attention to the Lisa in the final shot and hey, it's a prototype! (No Apple jewel on the back panel and no/hand written paper label on the PSU) |
18
on: April 17, 2024, 11:25:02 pm
|
||
Started by ried - Last post by ried | ||
19
on: April 13, 2024, 05:45:19 pm
|
||
Started by AlexTheCat123 - Last post by AlexTheCat123 | ||
Wow, thanks so much guys! It makes a lot more sense now!
|
20
on: April 13, 2024, 04:05:35 pm
|
||
Started by AlexTheCat123 - Last post by pablo_marx | ||
A rough translation of the decompression routine into JavaScript:
Code: [Select] const iconWidth = 48; I've included that and some compressed icons from the rev H boot sources here: https://codepen.io/pablo_marx/pen/zYXLNrO There'a a dropdown at the top to select the icon. That'll populate the text field with the bytes from the sources. Alternatively if I missed some icons in the sources, one should be able to paste the bytes into the text field. And any time the text field changes it should render the icon beneath the text field. And finally, one should be able to right click the icon and do Save Image As if they'd like to keep it. |